Unveiling the Excellence of Injection Molding Makers
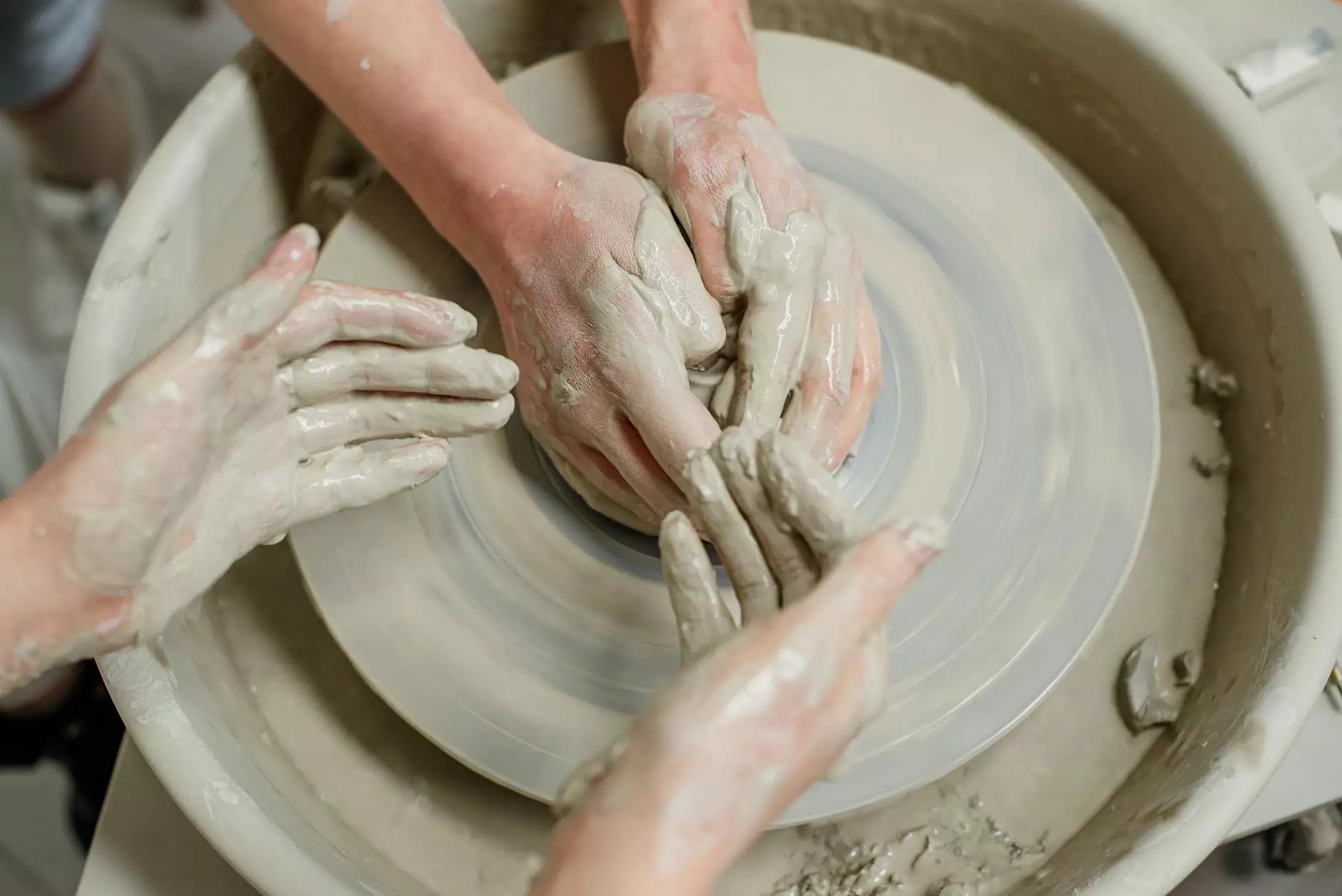
In today's fast-paced industrial environment, the importance of injection molding makers cannot be overstated. These professionals play a critical role in the manufacturing landscape, enabling businesses to produce precise, reliable, and complex components with remarkable efficiency. In this article, we will delve deep into the world of injection molding, emphasizing the innovative approaches and technologies utilized by industry leaders like DeepMould.
Understanding Injection Molding
Injection molding is a sophisticated manufacturing process that involves the injection of molten materials into a mold to produce a variety of parts and products. This method is widely used for creating components in industries such as automotive, consumer goods, medical devices, and more. Below are key aspects that highlight the significance of this method:
- Versatility: Injection molding can produce a wide range of products, from intricate and detailed parts to large-scale components.
- Efficiency: High-speed production cycles lead to lower manufacturing costs and quicker time-to-market.
- Consistency: Each product manufactured using this process maintains uniform quality and precision.
- Material Options: A variety of materials like plastics, metals, and composites can be used, offering flexibility based on application requirements.
The Role of Injection Molding Makers in Metal Fabrication
The role of an injection molding maker goes beyond the basic understanding of the process. These skilled professionals are at the forefront of innovation and technology in the metal fabrication industry. Let's explore the vital functions they serve:
Design and Prototyping
Injection molding makers often collaborate with designers and engineers to create molds that meet precise specifications. This involves:
- Utilizing CAD software to design intricate mold structures.
- Prototyping to test designs for functionality and durability.
- Iterating designs based on performance feedback, ensuring the final product meets all required specifications.
Material Selection
A major aspect of the injection molding process is selecting the appropriate materials. Here’s how injection molding makers excel in this area:
- They analyze the functional requirements of the final component, including strength, weight, and thermal characteristics.
- They keep abreast of the latest advancements in material technologies to offer innovative solutions.
- They ensure compliance with industry standards and regulations regarding material usage.
Advanced Technologies in Injection Molding
As manufacturing technology evolves, so do the techniques used in injection molding. Here are some of the cutting-edge technologies adopted by leading injection molding makers:
3D Printing for Mold Creation
3D printing is revolutionizing mold production. It allows for rapid prototyping and faster iterations of mold designs. This technology offers:
- Reduced Lead Times: Speeding up the design process by allowing for quick adjustments and validations.
- Cost-Efficiency: Lowering costs associated with traditional mold manufacturing methods.
- Complex Geometries: Enabling designs that were previously impossible with traditional techniques.
Smart Manufacturing and Automation
Implementing smart technologies enhances the injection molding process. Key benefits include:
- Increased Efficiency: Automating repetitive tasks reduces labor costs and human error.
- Data-Driven Decision Making: Collecting data from machines allows for real-time monitoring and adjustments.
- Greater Flexibility: Adapting production schedules to meet changing demands without major overhauls.
Quality Control in Injection Molding
Quality control is paramount in injection molding, given that even minor flaws can lead to significant issues in the final products. Here’s how injection molding makers ensure quality:
Inspection Techniques
Modern injection molding facilities employ advanced inspection techniques that include:
- Visual Inspections: Identifying visible defects during the production process.
- Dimensional Measurements: Using precision gauges and tools to ensure components meet specified dimensions.
- Non-Destructive Testing: Methods such as ultrasonic testing and radiography to detect internal defects without damaging the product.
Continuous Improvement Processes
Injection molding makers actively engage in continuous improvement processes to ensure the highest quality, which involves:
- Implementing Six Sigma and lean manufacturing principles.
- Regular training of employees on best practices and new technologies.
- Adopting customer feedback to refine processes and outcomes.
Benefits of Partnering with Leading Injection Molding Makers
Businesses seeking top-quality injection molding services can reap numerous benefits by collaborating with established injection molding makers like DeepMould.
Expertise and Experience
With extensive industry knowledge and hands-on experience, these experts guide clients through the entire injection molding process. This includes:
- Providing insights on cost-effective designs and materials.
- Predicting potential challenges and offering solutions to mitigate them.
- Delivering unparalleled customer service and support throughout the project lifecycle.
Accessibility to Advanced Technologies
By partnering with a leading injection molding maker, businesses gain access to state-of-the-art technology, such as:
- Advanced mold-making techniques.
- Innovative materials for improved performance.
- Automated systems for increased productivity and reliability.
Cost-Effectiveness
Utilizing the services of an experienced injection molding maker can lead to significant cost savings:
- Efficient production processes reduce waste and lower material costs.
- High-quality outputs result in fewer returns and product failures.
- Time-efficient project management leads to faster go-to-market timelines.
The Future of Injection Molding
The future of injection molding looks promising as new technologies and methods emerge. Here are a few trends shaping the industry:
Mass Customization
As consumer preferences shift towards personalized products, injection molding makers are expected to adapt by:
- Implementing flexible manufacturing processes that allow for customization without sacrificing efficiency.
- Investing in technologies that enable rapid changes in mold design and production outputs.
Sustainability Initiatives
With increased awareness of environmental issues, the injection molding sector is pushing for more sustainable practices by:
- Integrating recycled and eco-friendly materials into production processes.
- Minimizing energy consumption and waste throughout the manufacturing cycle.
- Adopting practices that reduce the environmental footprint of products.
Conclusion
In conclusion, the role of injection molding makers is vital in the realm of metal fabrication and manufacturing. Their contributions enhance product quality, reduce time-to-market, and facilitate innovation across various industries. With industry leaders like DeepMould at the helm, the future of injection molding promises to be bright, efficient, and sustainable. By stays informed and adaptable, these professionals continue to drive excellence in manufacturing for generations to come.
For businesses looking for a reliable injection molding maker, consider choosing partners who emphasize quality, innovation, and customer engagement. Such associations will undoubtedly yield superior products and contribute significantly to ongoing success in the competitive marketplace.