Understanding the Importance of Tooling Mold in Metal Fabrication
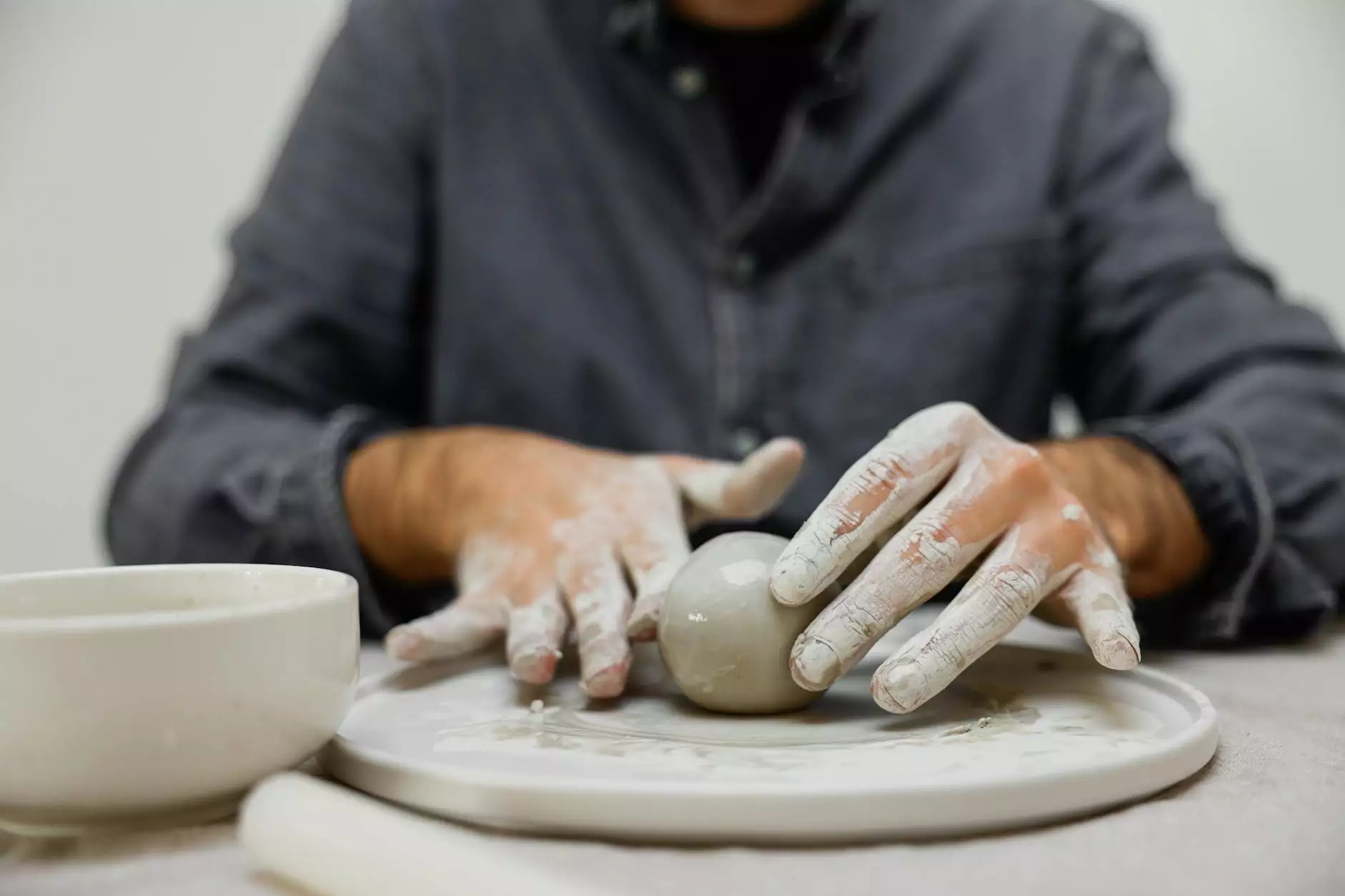
The tooling mold industry is an essential component of modern manufacturing processes, particularly in the field of metal fabrication. With the growing demand for precision-engineered parts, understanding how tooling molds function and their significance can help businesses optimize their production capabilities and maintain competitive advantages.
1. What is Tooling Mold?
A tooling mold is a specially designed tool utilized in the manufacturing process to shape materials into desired forms. It is mainly used in injection molding, die casting, and CNC machining. The accuracy and precision of these molds can significantly affect the quality of the finished products.
2. Key Benefits of Using Tooling Mold
- Enhanced Precision: Tooling molds are designed to create products with high dimensional accuracy, which is crucial for the manufacturing of intricate parts.
- Improved Efficiency: Utilizing molds helps streamline the manufacturing process by minimizing waste and reducing production times.
- Cost-Effectiveness: Investing in high-quality tooling molds can yield significant cost savings in the long run by reducing labor and material costs.
- Repeatability: Molds allow for the consistent reproduction of parts, ensuring that each product meets quality standards.
3. The Role of Tooling Mold in Metal Fabrication
In the realm of metal fabricators, the role of tooling molds cannot be overstated. They are fundamental for various applications, including:
3.1 Injection Molding
Injection molding is a process where molten metal is injected into a mold cavity. The tooling mold used in this process must be designed to withstand high temperatures and pressures, ensuring that the final product is formed accurately. This method is widely employed in the production of complex metal components.
3.2 Die Casting
Die casting is another common application of tooling molds. In this process, liquid metal is poured into a mold under high pressure. The precision of the die casting molds allows fabricators to create intricate designs that meet customer specifications efficiently.
3.3 CNC Machining
CNC machining often utilizes tooling molds to create templates for cutting metal parts. With a tooling mold, manufacturers can achieve near-perfect shapes and sizes, which helps in maintaining uniformity across production batches.
4. Types of Tooling Molds
There are several types of tooling molds that cater to specific manufacturing needs:
- Single Cavity Molds: Designed to produce a single part per cycle, these molds are ideal for less complex shapes.
- Multi-Cavity Molds: These molds can create multiple parts in one cycle, thus improving efficiency and reducing production costs.
- Family Molds: These molds are crafted to produce multiple parts of different shapes at the same time, which is beneficial for projects requiring variety.
- Hot Runner Molds: These systems maintain the temperature of the molten material, reducing waste and improving cycle times.
5. Designing Tooling Molds
The design process for tooling molds is intricate and must consider several factors, including:
- Material Selection: Choosing the right materials (e.g., steel, aluminum) for durability and heat resistance is crucial in mold design.
- Cooling Systems: Efficient cooling mechanisms are vital to control the temperature of the mold during production, affecting cycle times and product quality.
- Tolerances and Dimensions: Designers must maintain precise tolerances to ensure the final products fit correctly and function as intended.
- Manufacturing Process: The chosen manufacturing process will dictate the specific design elements required in the molding process.
6. Advancements in Tooling Mold Technology
With the advancement of technology, the tooling mold industry has seen significant improvements:
6.1 Computer-Aided Design (CAD)
CAD software allows for precise modeling and simulation of tooling molds, enabling engineers to identify potential issues before physical production begins.
6.2 3D Printing
3D printing technology is revolutionizing mold production by allowing for rapid prototyping and the creation of complex mold geometries that were previously impossible to achieve.
6.3 Smart Molding Technology
Integrating sensors into molds can provide real-time data on the manufacturing process, allowing for adjustments and ensuring optimal performance.
7. The Future of Tooling Mold in Manufacturing
As industries continue to evolve, the importance of tooling molds will remain critical. The focus will likely expand towards sustainability and efficiency:
- Sustainable Materials: Developing molds from recycled or eco-friendly materials will be essential for minimizing the environmental impact of manufacturing.
- Automation: Increased automation in mold making and production processes can enhance efficiency and reduce human error.
- Customization: As consumer demands shift towards personalized products, tooling molds will need to adapt quickly to accommodate bespoke manufacturing.
8. Conclusion
In conclusion, the significance of tooling mold in the metal fabrication industry cannot be overstated. They not only improve the efficiency and quality of production but also offer flexibility and adaptability essential for modern manufacturing. As businesses like DeepMould.net continue to innovate, understanding and utilizing the capabilities of tooling molds will be crucial for success.
By investing in high-quality molds and embracing new technologies, companies can position themselves at the forefront of the manufacturing landscape, ensuring they meet the demands of today and tomorrow.