Understanding GRP Modular Housings
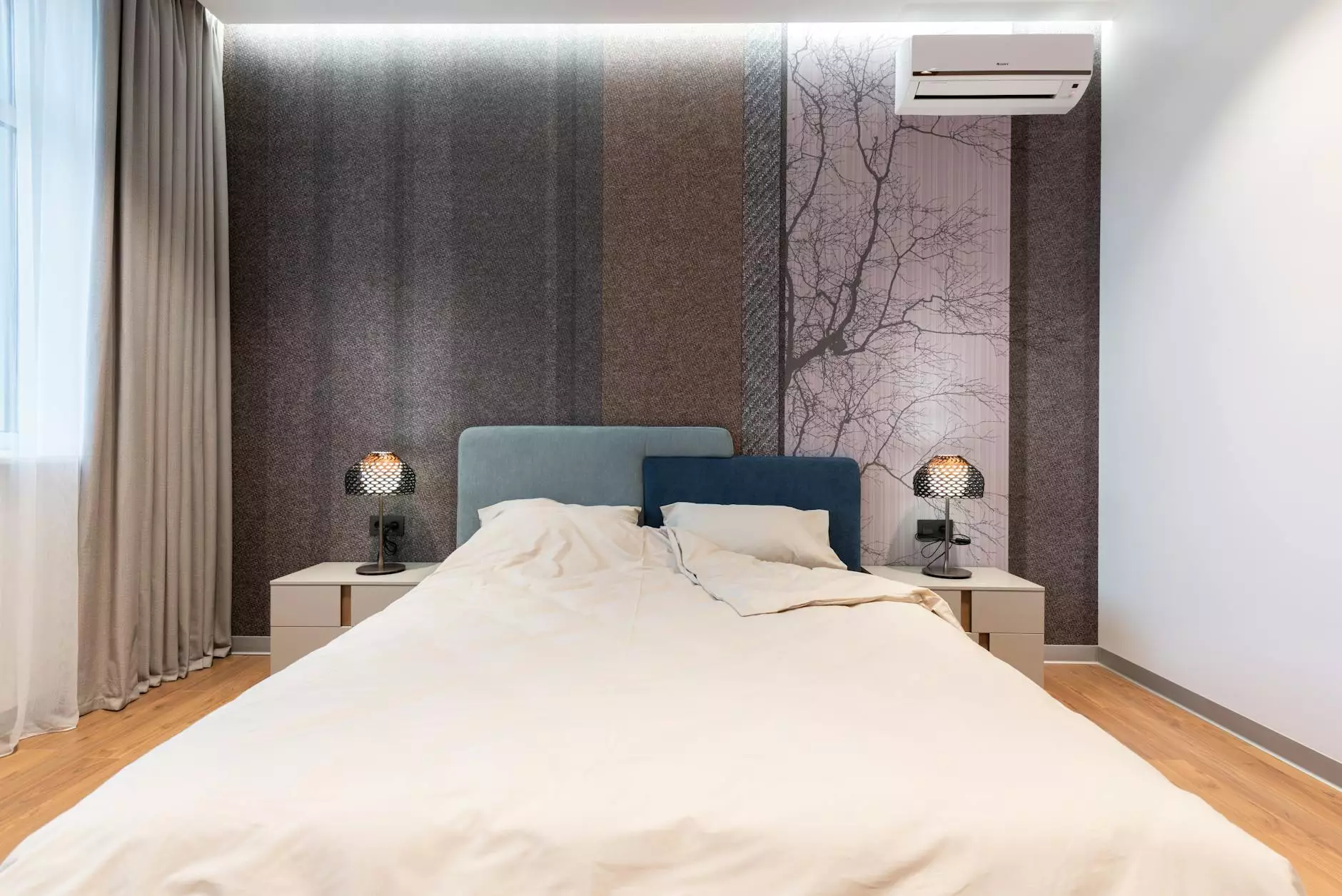
GRP modular housings represent an innovative solution in the construction and engineering sectors, providing an efficient way to create durable and versatile structures. This guide aims to delve deeply into the world of GRP modular housings, exploring their features, manufacturing processes, applications, and the inevitable advantages they offer over traditional materials.
The Evolution of GRP Technology
Glass-reinforced plastic (GRP) has emerged as a transformative material in various industries, thanks to its exceptional properties. To appreciate GRP modular housings, it is vital to understand the evolution of GRP technology itself:
- 1970s: GRP began to gain traction in sectors such as automotive and marine, where lightweight and corrosion-resistant materials were necessary.
- 1980s: The technology advanced, enabling the creation of more complex structures, leading to its implementation in the construction industry.
- 1990s-Present: Continuous advancements in composite materials led to the development of highly specialized GRP applications, including modular housings.
What Are GRP Modular Housings?
GRP modular housings are specifically designed enclosures made from glass-reinforced plastic. These housings can be prefabricated and assembled on-site, making them an attractive option for a variety of applications. Their modular nature means that they can be easily adapted, extended, or reconfigured as needs change.
Key Characteristics of GRP Modular Housings
The success of GRP modular housings can be attributed to a range of beneficial characteristics:
- DURABILITY: GRP is resistant to extreme weather conditions, chemicals, and UV radiation, ensuring long-term performance.
- LIGHTWEIGHT: Compared to traditional materials like steel or concrete, GRP is significantly lighter, which simplifies transportation and installation.
- COST-EFFECTIVENESS: The reduction in labor and construction time translates to lower overall costs.
- AESTHETICS: GRP can be molded into various shapes and colors, providing flexibility in design.
Manufacturing Processes of GRP Modular Housings
The creation of GRP modular housings involves specialized manufacturing processes to ensure that the materials meet industry standards. Here’s how it works:
1. Material Selection
The quality of the raw materials used is critical. High-grade glass fibers combine with resin to form the composite material used in GRP.
2. Molding Techniques
Various molding methods, such as hand lay-up, spray-up, and vacuum infusion, can be employed. Each method offers unique advantages, often regarding strength and finish quality.
3. Curing Processes
After molding, the structures undergo a curing process, where chemicals in the resin react to form a solid, durable structure. Curing can be conducted at room temperature or under controlled heat conditions.
4. Finishing Touches
Once cured, the final touches include surface finishes and protective coatings to enhance durability and aesthetics.
Applications of GRP Modular Housings
The versatility of GRP modular housings allows them to be deployed across a wide range of industries. Here are some prominent applications:
- Telecommunications: Used for housing sensitive electronic equipment, providing a controlled environment.
- Utilities: Ideal for electrical substations and storage for renewable energy components.
- Waste Management: Effective as enclosures for pumps and treatment facilities.
- Construction: Adopted as site offices, storage spaces, or even as temporary living quarters.
The Advantages of GRP Modular Housings
Employing GRP modular housings presents numerous advantages over traditional building methods. Here’s a closer look:
Flexibility and Scalability
One of the most notable benefits is the modular nature of GRP housings. They can easily be scaled or reconfigured to meet changing requirements, making them an excellent choice for evolving projects.
Reduced Installation Time
The prefabricated nature of GRP modular housings allows for quicker installation compared to conventional constructions, rapidly bringing projects to completion.
Environmental Benefits
GRP is often manufactured with a lower carbon footprint than traditional building materials. Moreover, its longevity reduces the need for replacements, contributing to sustainability.
Low Maintenance Requirements
GRP does not require frequent maintenance, saving time and money for businesses. Its resistant properties mean that it retains its structural integrity longer than many alternatives.
Future Trends in GRP Modular Housing
The demand for GRP modular housings is expected to grow as industries lean towards more efficient, sustainable methods of enhancing their infrastructure. Emerging trends include:
- Advancements in Material Science: Continuous research into enhancing the properties of GRP will result in even more robust and versatile modular solutions.
- Smart Technologies: Integration of smart technology for monitoring environmental conditions within GRP housings to enhance safety and efficiency.
- Increased Customization: Tailored solutions will become more commonplace, allowing for unique designs to meet specific client needs.
Conclusion
In conclusion, GRP modular housings represent a forward-thinking approach to traditional building methods. With their unparalleled benefits, applications across diverse industries, and future potential, businesses aiming for efficiency, durability, and adaptability should consider this innovative solution.
For more information and inquiries about GRP modular housings, visit Celtic Composites and discover how these advanced structures can revolutionize your project today!